Tubing That Performs Under Pressure: What to Know Before Your Next Equipment Upgrade
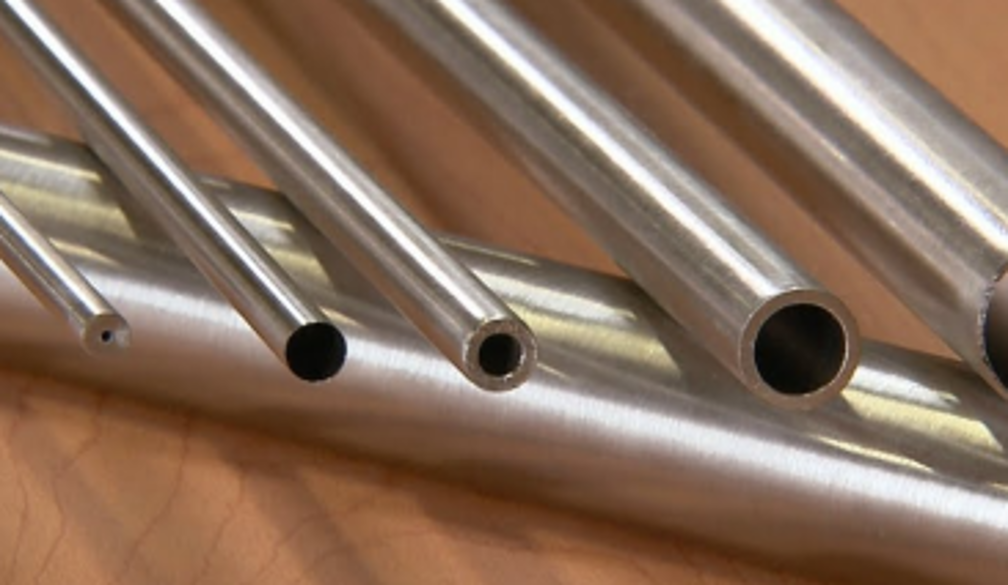
More and more professionals are turning to high-grade stainless steel tubes for their flow systems, particularly when pressure, temperature and cleanliness must be maintained at all times.
In industries where hygiene, durability and performance are non-negotiable, choosing the right tubing isn’t just a detail—it’s a decision that can make or break your system. Whether you're brewing, bottling, pasteurising or cleaning, the humble tube plays a central role in keeping operations running smoothly. That’s why more and more professionals are turning to high-grade stainless steel tubes for their flow systems, particularly when pressure, temperature and cleanliness must be maintained at all times.
If you’re preparing for an equipment upgrade, or scaling production to meet demand, knowing what to look for, and who to source from, can save you time, money, and future headaches.
Strength in the Details: Why Stainless Steel Matters
Not all materials are created equal when it comes to industrial tubing. When you're handling hot liquids, corrosive chemicals or cleaning agents like caustics and steam, plastic or low-grade metals simply won’t hold up. That’s where stainless steel tubes offer a clear advantage.
Manufactured from 316 or 304-grade stainless steel, these tubes are engineered to resist corrosion, endure high temperatures, and maintain structural integrity under significant pressure. In food and beverage applications especially, stainless steel is the go-to for hygienic design. A polished internal finish allows for easy cleaning and prevents product build-up, making it a crucial part of Clean-In-Place (CIP) and Sterilise-In-Place (SIP) systems.
Tubes with mirror or sanitary polish finishes not only improve flow but also help eliminate micro-pockets where bacteria might hide, something that is essential in both brewing and dairy processing environments.
Matching Tubing to System Demands
As production lines become more complex, tubing must do more than just connect point A to B. It has to integrate seamlessly with fittings, valves, pumps and tanks while accommodating pressure changes, thermal cycling and constant flow. Precision-welded stainless steel tubes with consistent wall thickness and high tolerance levels reduce the risk of weak points or flow disruption.
For breweries, wineries or distilleries, tubing must be compatible with a wide variety of accessories, from tri-clamp fittings and butterfly valves to carbonation stones and pressure gauges. Choosing the right tubing ensures that every part of your system works together without leaks, contamination, or bottlenecks.
This is where partnering with experienced stainless steel pipe suppliers becomes essential. Reliable suppliers offer more than just raw materials, as they provide expert guidance, product compatibility, and access to a wide inventory of sizes and finishes suited to your specific process.
Looking Beyond the Basics: Why Supplier Quality Counts
Upgrading your equipment often starts with reviewing existing infrastructure. If your piping has become difficult to clean, prone to corrosion, or no longer meets capacity requirements, it’s probably time to make the switch. But sourcing the right replacement is only part of the equation. The reliability of your stainless steel pipe suppliers can influence lead times, quality assurance, and ongoing technical support.
Top suppliers ensure that their tubing meets industry standards, comes with proper certifications, and is cut, finished, and shipped with care. Some also offer additional services like fabrication support, custom fittings, and audits to help you assess your current setup.
Preparing Your Operation for the Future
Investing in the right tubing now will pay off long-term. High-grade stainless steel tubes withstand years of wear, support demanding cleaning protocols, and keep your operation compliant with food safety standards. By choosing a system built to perform under pressure, and sourcing from trusted stainless steel pipe suppliers, you can set your production up for smoother workflows, fewer failures, and more consistent results, no matter what’s flowing through your lines.